Article paru dans le Bioénergie International n°63 d’octobre 2019
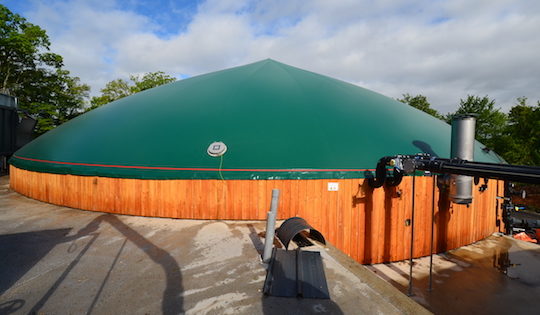
L’un des deux digesteurs chez Méthacycle, photo Frédéric Douard
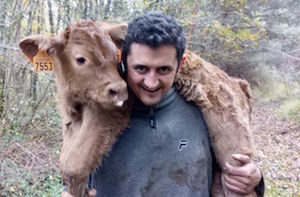
Jules Charmoy, photo Gaec des Charmes
La ferme biologique des Charmes est située sur la commune de Saint-Aquilin à quelques kilomètres de Périgueux, préfecture du département de la Dordogne. Elle a été reprise en 1999 par Jules Charmoy qui l’a convertie à l’agriculture biologique. L’activité est principalement basée sur la production de viande de vaches allaitantes de race limousine et de cochons de plein air, commercialisée en direct et en circuits courts.
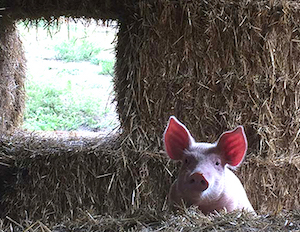
Des animaux heureux, ici dans un cabane en paille, photo Gaec des Charmes
L’exploitation compte aujourd’hui 230 ha dont grossièrement les deux tiers en céréales, un tiers en herbe et 16 ha en noyers. La production de céréales, qui est stockée à la ferme, est dédiée à la vente, à l’alimentation du cheptel et à la production de pain. Les 400 tonnes de paille de céréales produites par an rendent l’exploitation autonomie en litière. Avec ses deux salariés, Jules cultive également des légumineuses pour l’apport protéique à ses bêtes, mais aussi des lentilles, du tournesol et des noix.
Les biocarburants pour commencer
Dès le début de sa carrière d’agriculteur, Jules, fidèle à ses convictions écologiques, participe au montage d’un groupement d’agriculteurs, réunis en coopérative d’utilisation de matériel agricole (CUMA), pour produire de l’huile végétale pure à partir de tournesol, pour faire fonctionner les tracteurs et autres véhicules des exploitations. Cette filière de valorisation permet aussi de produire en autonomie du tourteau et donc des protéines pour les animaux.
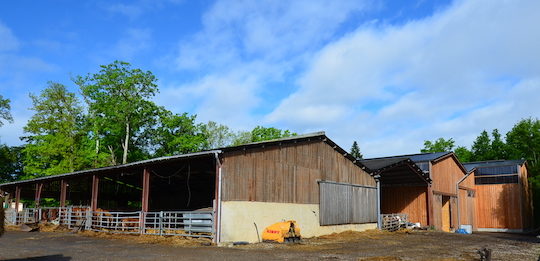
Les bâtiments d’élevage du GAEC des Charmes, photo Frédéric Douard
À partir de 2006, c’est du biodiesel qui est produit à partir de graisse de canard et de bœuf, d’huile de friture usagée, en parallèle avec le projet Valagro à Melle et qui prendra fin en 2017. À Saint-Aquilin, la production de biodiesel continue mais uniquement en autoconsommation car, encore aujourd’hui les choix politiques verrouillent le développement de ces filières courtes en provenance des producteurs agricoles.
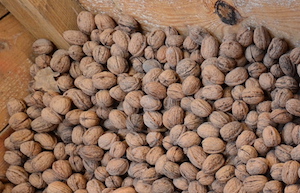
Les noix du GAEC des charmes, photo Frédéric Douard
Ce sont ainsi 50 m³ qui sont produit annuellement à partir de tournesol, et qui alimentent tracteurs et engins mais aussi le four à pain. La production de pain biologique, produit avec les céréales de l’exploitation, a commencé en 2014 et fournit marchés, magasins et collectivités.
Et en 2019, avec la mise en service de l’unité de méthanisation, la production de bioGNV est prévue et va faire l’objet d’un projet avec financement participatif !
Le bois-énergie pour diversifier
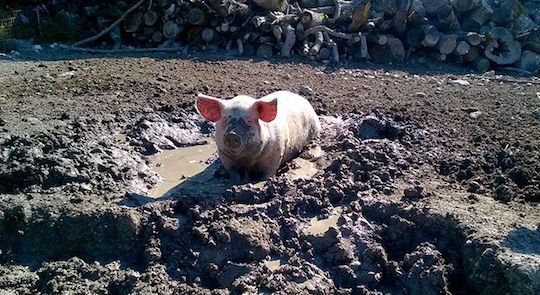
Cochon en plein air et stock de bois-énergie, photo GAEC des Charmes
En 2004, Jules, qui bien sûr se chauffe déjà au bois-bûche, se met aussi à produire du bois déchiqueté dans le cadre de la CUMA EPS, l’une des trois CUMA bois-énergie de Dordogne. Forte de 45 adhérents, elle est équipée d’une déchiqueteuse Pezzolato 900-660 avec grue Palfinger et qui peut passer des bois jusque 40 cm de diamètre. Dans ce département très boisé, notamment de châtaigniers et de chênes, les plaquettes produites alimentent les chaudières des agriculteurs adhérents à la CUMA. Puis très vite une Sarl est créée pour commercialiser ce combustible renouvelable, et c’est la naissance d’Agrocycle.
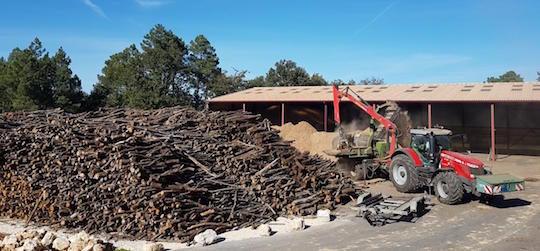
Jules Charmoy produit du bois-énergie en CUMA depuis 2004, photo Agrocycle
Les plaquettes sont produites en deux dimensions : 30 mm pour les petites chaufferies, et 100 mm pour les grandes comme celle de l’hôpital de Périgueux. Une bonne partie de la production est criblée pour garantir un bon fonctionnement en évitant les sur-longueurs et l’excès de fines.
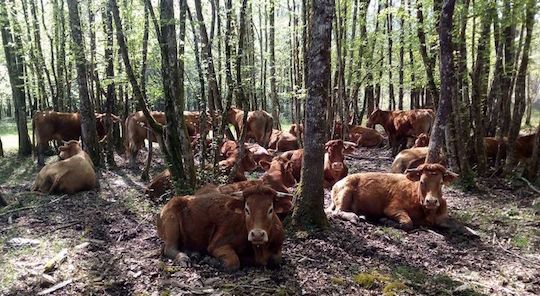
Le GAEC des Charmes ne manque pas de bois sur l’exploitation, ici le troupeau de boeufs limousins au bois, photo Gaec des Charmes
Filiale de la fédération départementale des CUMA de la Dordogne, la Sarl commerciale la production de toutes les CUMA du département, hors consommation des adhérents. Agrocycle, c’est aussi la production de compost à partir de déchets verts, pour enrichir et préserver les sols.
Le biogaz pour consolider
En 2012, Jules et plusieurs de ses collègues agriculteurs, qui veulent compléter l’autonomie de leur exploitation, mais aussi réduire leurs charges et se renforcer économiquement, lancent le projet Méthacycle. Dix exploitations se regrouperont autour du projet pour atteindre un volume suffisant d’intrants.
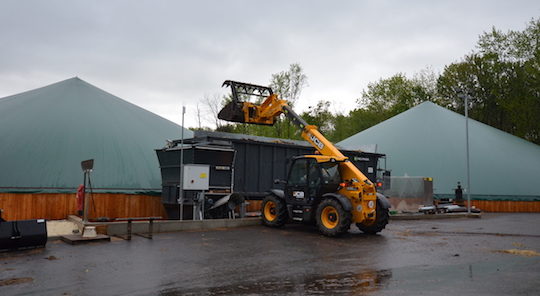
Le chargement de la ration chez Méthacycle, photo Frédéric Douard
Le troupeau de la ferme des Charmes est composé de 80 mères, deux taureaux, 30 génisses pour le renouvellement et 90 animaux à l’engraissement. Bien que les animaux passent une grande partie de l’année à l’extérieur, la quantité de fumier disponible sur l’exploitation est de 1 800 tonnes par an. Le fumier des cochons, 130 tonnes par an, est quant à lui épandu après compostage, car il contient beaucoup trop de corps étrangers, les cochons ayant toute liberté d’aménager leur logis avec tout ce qui leur plaît !
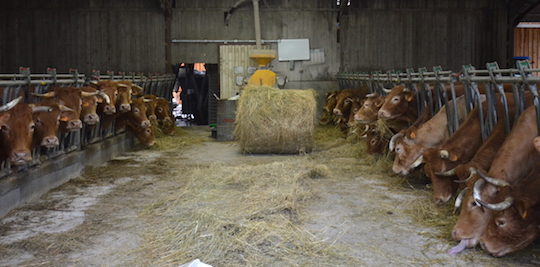
Le troupeau de vaches limousines allaitantes du GAEC des Charmes, photo Frédéric Douard

Vaches au pré, photo GAEC des Charmes
Le tonnage nécessaire au bon fonctionnement est apporté par sept exploitations agricoles et quatre entreprises pour un tonnage annuel d’environ 11 000 tonnes :
- 4 000 tonnes de fumier bovin,
- 600 tonnes de fumier de volaille,
- 900 tonnes de fumier de cheval, avec échange de paille,
- 1 800 tonnes de CIVE en couverture des zones vulnérables : 70 ha d’hiver (Seigle, trèfle de Micheli …) et 70 ha d’été (Sorgho, trèfle d’Alexandrie …),
- 1 000 à 1 500 tonnes de drêches de maïs doux,
- 500 tonnes d’issues de céréales bio de la CORAB,
- 1 800 m³ de lactosérum de brebis et de chèvre de la fromagerie bio Chêne Vert,
- 200 tonnes de tontes de pelouse d’Agrocycle.
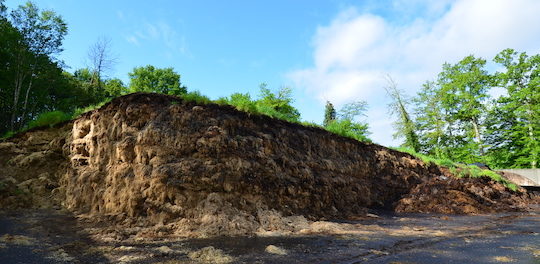
Silo à CIVE chez Méthacycle, photo Frédéric Douard
Des infrastructures ont été construites pour le stockage des instants : une cuve de 220 m³ pour le lactosérum et une plateforme de 4 000 m² en enrobé pour les solides dont 1 000 m² traités pour les produits acides. Pour éviter le plastique, la couverture des silos d’intrants est assurée par de la paille semée d’orge.
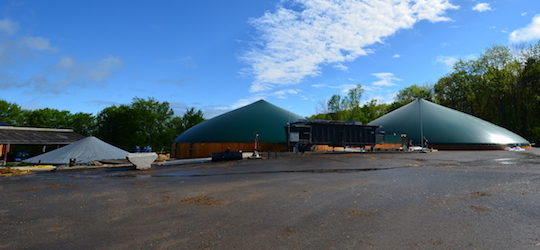
Les trois cuves et la plateforme enrobée de Méthacycle, photo Frédéric Douard
Les installations de méthanisation ont été fournies par agriKomp. Et comme les sols du secteur comportent énormément de cailloux qui se retrouvent fatalement dans le fumier, il a été décidé de ne pas mettre de piège à cailloux, ce qui aurait occasionné des interventions trop fréquentes : un curage des cuves sera à envisager périodiquement.
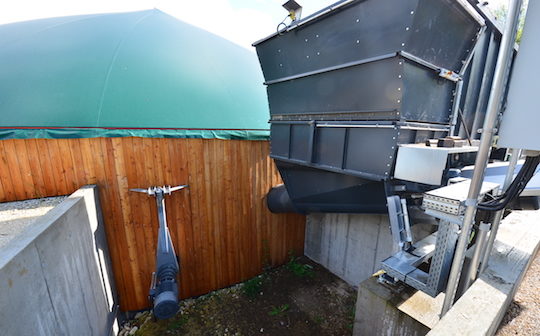
Gros plan sur la zone d’introduction des intrants dans le digesteur agrikomp, photo Frédéric Douard
Autre conséquence de ce choix, l’incorporateur de 45 m³ introduit la matière directement sans broyage. Ce choix induit une petite perte de production de gaz, mais qui présente deux avantages : la quasi-diminution des risques de blocage, les matières étant véhiculées par pompes à queue de cochon, et un taux de matière organique plus fort dans le digestat, positif pour les sols.
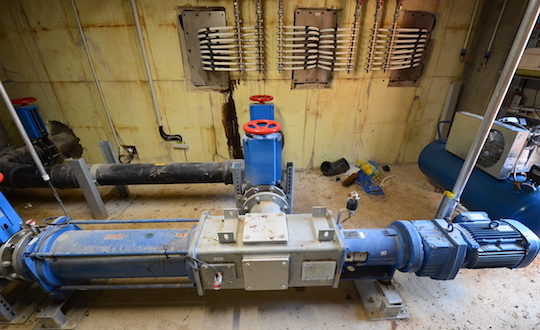
La pompe de circulation WANGEN chez Méthacycle, et à l’arrière le circuit de chauffage du digesteur, photo Frédéric Douard
La digestion a lieu à 47 °C dans un digesteur de 2700 m³. Elle se termine dans un post-digesteur de même volume. Le digestat brut est stocké dans une cuve de 5500 m³ enterrée à moins huit mètres.
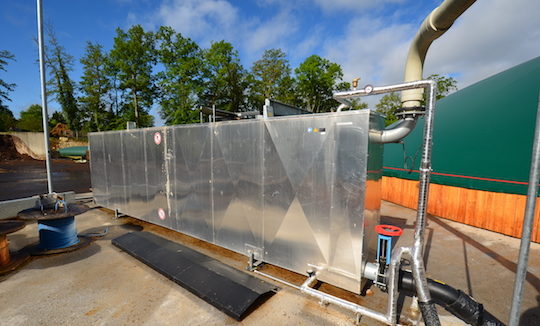
L’hygiéniseur d’intrants chez Méthacycle, photo Frédéric Douard
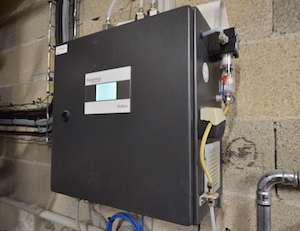
Le boitier d’analyse du biogaz FRESENIUS chez Méthacycle, photo Frédéric Douard
Entre le post-digesteur et la cuve de stockage, le digestat passe par un traitement thermique dans un équipement appelé Cooker, pour garantir la destruction d’éventuels germes de tuberculose bovine avant épandage, le département dénombrant une vingtaine de cas par an. Ce traitement à 70 °C durant une heure permet aussi de neutraliser totalement les graines d’adventices, un élément important dans une exploitation biologique.
La maintenance des installations de méthanisation et le suivi biologique de la digestion sont assurés par la société Service Union. L’investissement total du projet méthanisation se monte à 2,6 M € plus 0,7 M€ pour le bâtiment et le système de séchage.
Valoriser l’énergie du cogénérateur et du soleil
La transformation du biogaz en énergie est réalisée dans un moteur agriKomp BGA222 qui a été mis en service le 18 mars 2019. La production d’électricité de 300 kW génère une production annuelle de 2,4 GWh, rémunérée 21,75 €/MWh. Dans le local de cogénération, une place est d’ores et déjà prévue pour un second moteur.
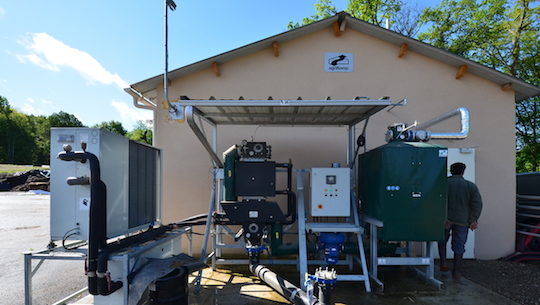
Le local de cogénération, photo Frédéric Douard
Sur le moteur sont également récupérés 2,4 GWh de chaleur par an. 800 à 900 MWh/an sont utilisés dans le chauffage du processus, principalement en hiver, le reste est valorisé en séchage. Le bâtiment de séchage, qui sert également de grange à foin, est équipé d’un double toit qui récupère la chaleur solaire par un système de ventilation.
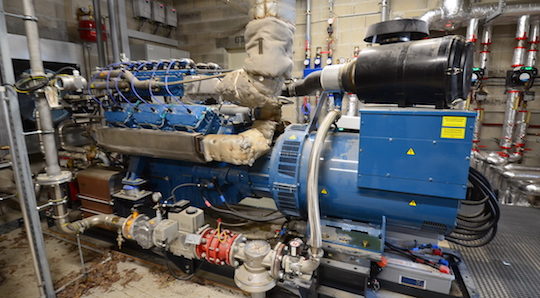
Le moteur de cogénération Doosan, photo Frédéric Douard
Équipé de grilles Les Mergers, le séchoir multi-produits a séché son premier foin le 1er mai 2019. L’installation de 1080 m² a été conçue pour sécher du foin (600 tonnes sur l’exploitation), et des céréales et du bois-énergie (plus de 3000 tonnes par an) pour les exploitations des associés mais aussi en prestation. L’objectif de Jules est de ramener l’alimentation de ses bovins à l’herbe, de manière à vendre une plus grande part de céréales. En 2018, sur sa production de 400 tonnes, ses bovins lui en avaient mangé 150 tonnes, en 2019 grâce au séchage, ce sera 50 tonnes seulement, et ensuite encore moins.
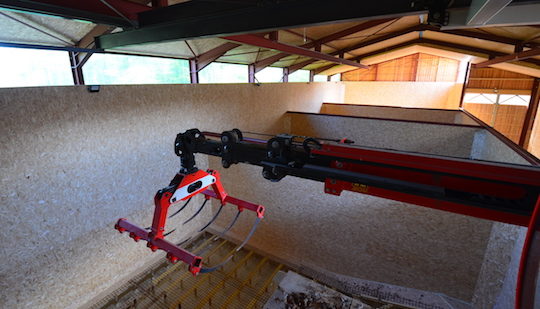
La nouvelle grange à foin avec sa grille et son plancher sécheur, photo Frédéric Douard
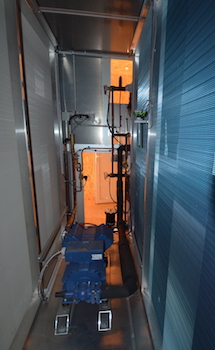
Le système de déshumidification de l’air de séchage, photo Frédéric Douard
Et comme cette installation est aujourd’hui la seule du département exclusivement en bio, la coopérative locale, la CORAB, l’utilise pour le séchage de son tonnage bio, qui n’est ainsi pas contaminé dans le séchoir des céréales chimiques. Comme autre débouché à la chaleur, Jules étudie aussi le traitement thermique de cagettes en bois pour fruits et légumes bio, un passage à 56 °C qui détruit les insectes.
Notons sur la partie technique, que l’air de séchage est déshumidifié avant circulation dans les matières, par un système thermodynamique à condensation, qui génère lui aussi de la chaleur à hauteur de 30 kW. Avec les 150 kW du moteur et les 150 kWc du toit solaire, ce sont ainsi jusque 330 kW de chaleur qui sont ainsi disponibles aux belles heures pour le séchage.
Le digestat
Le digestat est épandu brut tout au long de l’année sur les parcelles des agriculteurs apporteurs, selon les besoins : en janvier sur l’orge, en février sur les prairies, en mars sur le tournesol et le maïs, en juin sur la luzerne et le ray-grass, en juillet sur les semis de CIVE derrière les moissons, en août avant les semis de céréales… Une tonne à pendillards est utilisée pour l’épandage sur les cultures, alors que l’épandage sur prairies requiert une rampe avec enfouisseur. Signalons enfin que les CIVE sont implantées en semis direct.
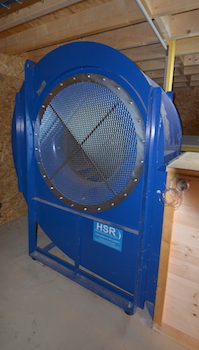
La centrale de ventilation du sécheur, photo Frédéric Douard
Contacts :
- Méthacycle – Gaec des charmes : Jules Charmoy / +33 553 037 997 / +33 673 64 00 50 – www.gaec-des-charmes.com
- Agrocycle : Rodolphe Deffieux / +33 608 254 581
- Méthanisation et cogénération : +33 254 561 857 – info@agrikomp.fr – www.agrikomp.com
- Cuves et bâtiment de séchage : www.wolfsystem.fr
- Séchage : HSR – www.heutrocknung.com
- Grilles de séchage à plat : lesmergers.fr
- Maintenance : +33 245 940 016 – info@serviceunion.fr – www.serviceunion.fr
- Pompe Biomix Wangen : +33 384 927 676 – www.agriest.com – www.wangen.com
- Analyseur biogaz : info@fresenius-ut.com – www.freseniusinstruments.com
- Déchiqueteuse : Marc Reinhardt / +33 472 793 223 – marc@pezzolato.fr- www.pezzolato.fr
Frédéric Douard, en reportage à Saint-Aquilin